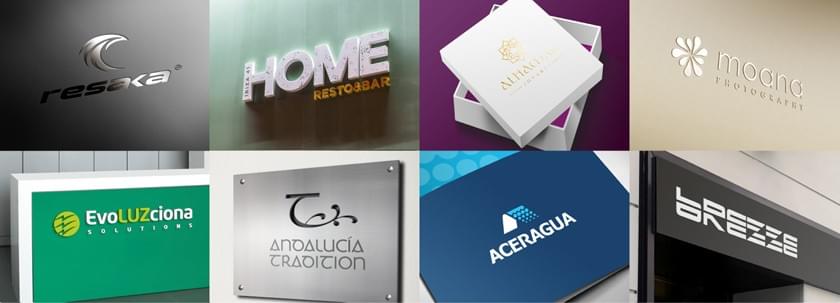
You already have your logo or your corporate stationery in a folder on your computer, but ... Now what?
Surely you wonder what are the different techniques, finishes or materials that exist to get the most out of your logo or your business cards. Surely sooner or later you need a license plate for your business, an illuminated sign or label a vehicle ...
To resolve all the doubts that arise at this time we wanted to write this article. We want to guide our clients about the different possibilities that exist and that from the beginning they have the ability to choose which is the best option for their business or product.
Next we are going to take a tour of the different techniques that exist. As there are many, we are going to divide them according to the support or application that we are talking about: Stationery, plates, signage, corporeal letters, etc ...
STATIONERY
1. Paper type:
When printing your corporate stationery, the first thing you will think about is: What type of paper do I choose? In general, there are some "standard" paper brands that all printers know because they are the ones they use in 80% of their corporate stationery orders. They are white paper and cardboard without textures, they give a good result and are cheap. These are “Bond” or similar paper in the case of folios or envelopes (papers with less thickness) and “Couché” paper in the case of thicker papers (weight) such as business cards or folders. If you want a good result and you don't want to spend a lot of money, these types of papers are perfect.
If you want or can spend a little more money, you can ask the printer to show you paper samples. There are many types, and the fundamental difference with respect to the previous ones is the type of texture it has. The best known is the “laid” paper, which is that which has transverse lines or filaments that give it a high quality appearance. There are also recycled type papers, with metallic reflections, etc ... If you are thinking of a special paper for your stationery, it is best that you go to a good printing company and they show you some examples and give you a price.
In logo design hill - logodesignhill.us in general we are not very fond of looking for "very special" papers, we prefer to work on a "standard" paper so that the leading role is in the design (not on the paper), or in any case, show off the design through finishes that can be applied on paper such as heat-sealed, laminated, etc ...
2. Finishes:
- Spot Inks:
This is just a small mention so you know that your stationery can be printed in CMYK or Pantone colors , it depends on whether you are going to use a digital printing press (cheaper for small runs and of acceptable quality) or Offset printing (better quality and more profitable for large print runs: from 500 units). CMYK colors will always be worse printed than PANTONE colors (the most universal color guide that exists, although there are others). The reason for this difference in quality lies in the way of printing. We are not going to go into technical details now, but PANTONE colors leave more compact, more uniform masses of color with greater vividness and intensity.
- Metallic inks:
The metallic effect can be achieved by using a certain range of Pantone colors, the “Metallic”. It is a range of conventional colors to which certain pigments have been added to achieve a metallic shine. The advantage of this system over others is that the cost increase is very small but it has the disadvantage that the metallic effect is very subtle, it is not as impressive as heat sealing.
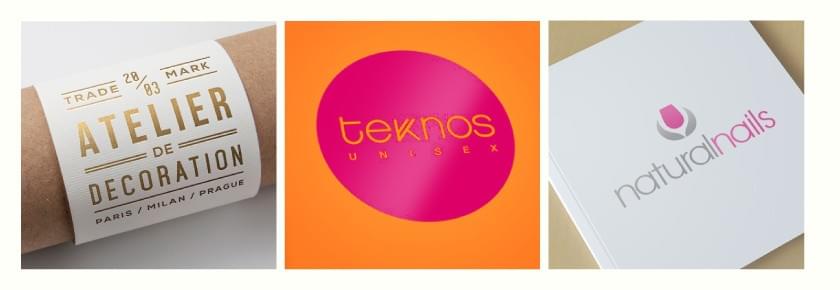
- Metallic heat sealing:
Heat-sealing or metallic “Stamping” is a finishing process by which we manage to transfer a metallic-looking film to paper thanks to a combination of heat and pressure. This type of finish is frequently found on the labels of high-end products such as certain wines and other alcoholic beverages (whiskey, gin, etc ...).
The effect it gives is spectacular and conveys an idea of great quality and professionalism.
The two disadvantages that it has is that it often does not allow you to print very small details and above all that it is more expensive than a conventional printing.
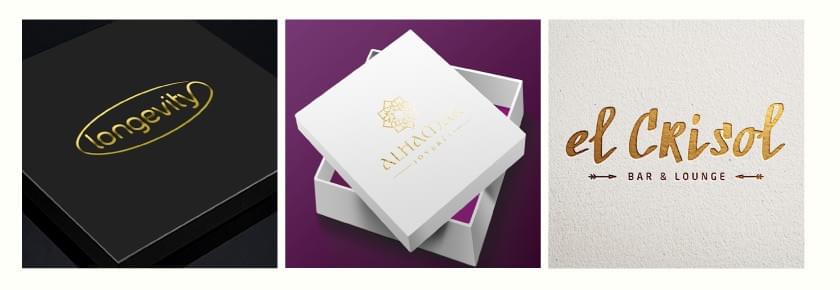
- Glossy or Matte laminated:
Laminating or laminating consists of adhering a very thin plastic sheet to the surface of a paper, (for example: business cards, a folder, etc ...).
This very thin plastic layer achieves a finish with a smooth texture to the touch and contributes to the durability of the work, since it protects the paper from external agents such as humidity, grease or the passage of time. In addition, in the case of matte lamination we achieve a very elegant and professional-looking finish. The advantage of this system is that the over-cost is quite small. The drawback is that it has its limitations: the lamination is done to the entire surface as a whole, we cannot apply it only to certain elements to highlight them as it happens with UVI varnish.
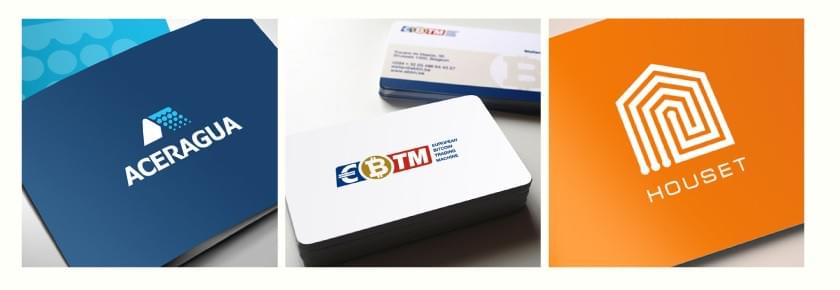
- UVI varnish:
UVI varnish is like a layer of glossy varnished paint that, applied to a specific area of the design, gives the whole a sophisticated and highly professional touch. It can be applied by Offset (traditional printing) or screen printing.
-Offset: it is done using a 5-body machine (4 inks + varnish), printing everything at the same time and drying it using ultraviolet light (UVI).
-Screen printing: The varnish is applied two days after having printed the paper, once it is completely dry.
The screen printing varnish gives a much brighter and higher quality result. It also allows us to apply it on paper that has already been printed and laminated, which allows us to make spectacular finishes thanks to the contrast between the matte laminate that covers the entire paper and certain elements that we want to highlight with the gloss varnish.
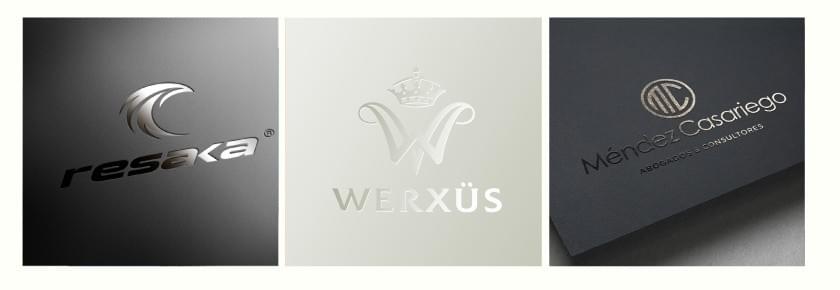
- Reliefs or "dry hit":
The technique of dry blow allows to give a relief to a certain area of our design, for example, if we want to highlight the logo in a folder we can go to this system and we will achieve a very professional finish. To use this system, you have to make two molds (female and male) and by means of pressure we manage to trap the paper between the male and the female, getting the paper to be marked with this relief. The type of relief can be high relief or low relief depending on whether we want the paper to sink or protrude. Generally, the relief is applied on an already printed area, for example a logo, which requires great precision so that the "dry hit" coincides with the printed area and not a few millimeters beyond (off-center).
The drawbacks of this system are several:
- The cost overrun.
- We cannot emboss on very fine papers because they would break, always from 100 grams.
- We cannot make reliefs in very small details
- We have to be careful that on the back of the area that is embossed there is not very small text or some important element that can be distorted by the relief.
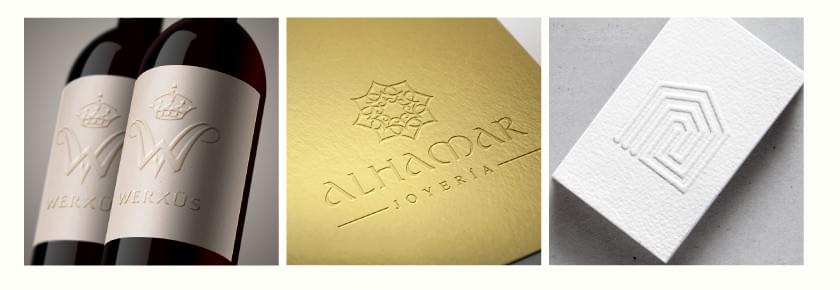
- Dies:
The die-cutting of a paper consists of perforating a paper or giving a certain shape to its outline.
-With punching machine: It is the traditional system that consisted of creating a mold with a certain shape and perforating the paper by pressure. The smaller the shape or the tighter curves, the more difficult it will be to make this die.
-With laser: It is a much more modern procedure that allows us almost total freedom when stamping and making all kinds of cuts on paper without the restrictions that the classic stamping machine had.
The big drawback of the dies is the cost and also how delicate it is to have a cut paper (it can break). The great advantage is the result: it can be spectacular and we will achieve an image that will attract attention in front of the competitors.
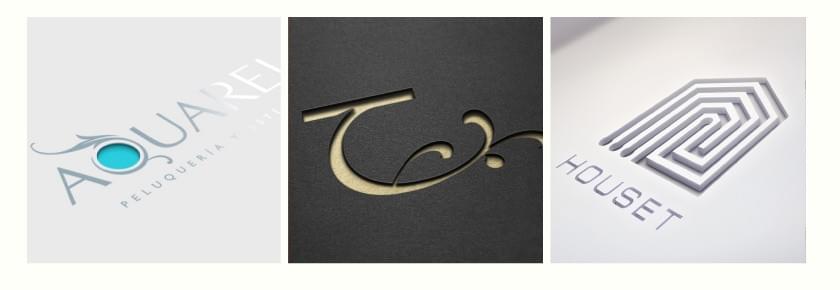
- Silkscreen:
It is the most comprehensive printing technique and one of the oldest. Screen printing allows us to print almost on any material with spectacular color quality. We can print on fabric, leather, ceramic, metal, paper and a long etc ... It also doesn't matter if the color of the surface is dark, since the ink covers it completely.
The principle of screen printing is based on the application of color through different tensioned meshes (one for each color) on the surface that we want in the areas where there is no previously applied varnish.
Although many of the processes have been mechanized, it still retains a fairly handcrafted part, which makes it a rather expensive technique, although of a quality without competition.